CLIMECH INDIA - Engineered Dehumidifier
Our Engineered Dehumidifiers are available as standard units as well as packaged with pre-cooling, after-cooling, heating, heat recovery etc. for the most cost efficient environment control in various industrial applications.
Units are designed with custom configurations of standard components to meet unique project requirements. Total system integration is also available inclosing heating, cooling, bye-pass, pre filter for complete air handling and environment control needs.
1. High Quality
2. Hygienic Design
3. Easy to Assemble on Site
4. Commissioning by our Skilled
Service Engineers
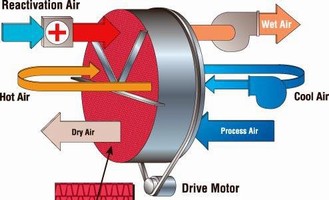

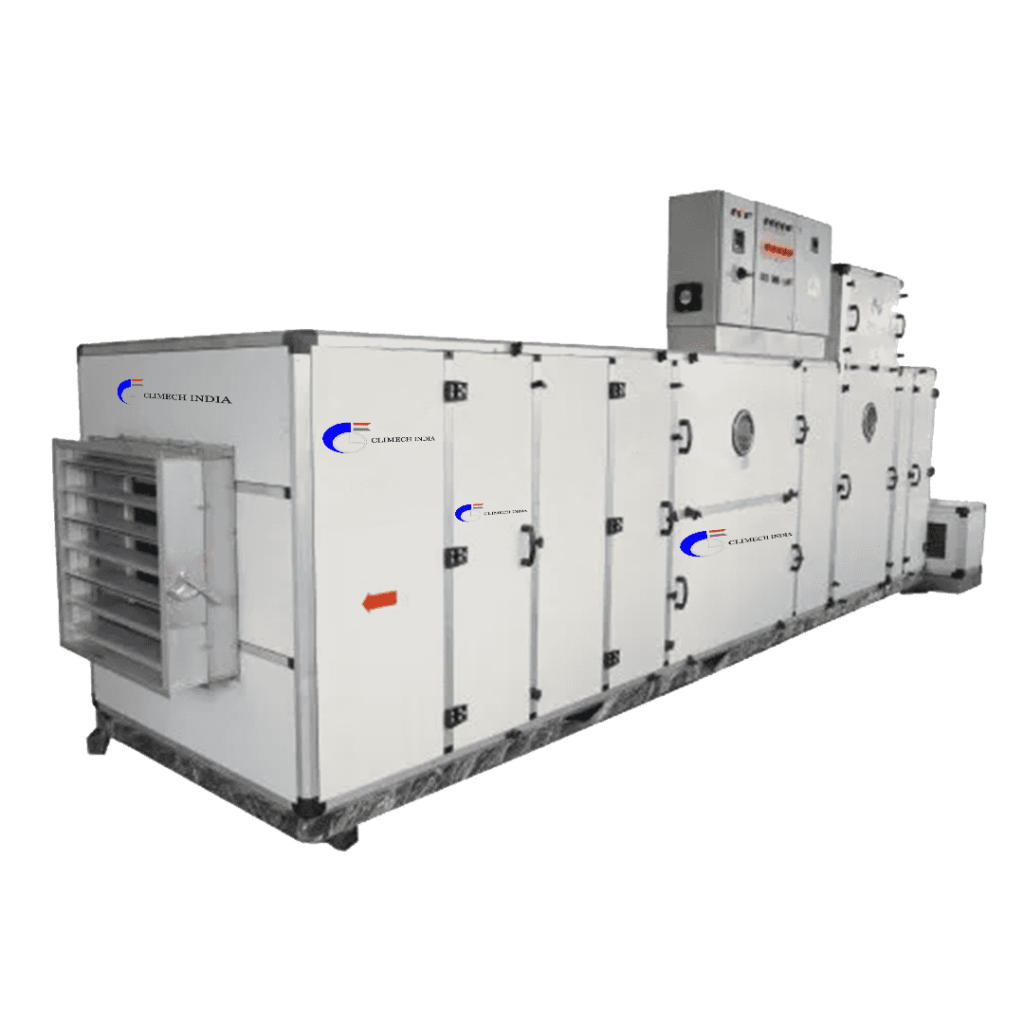
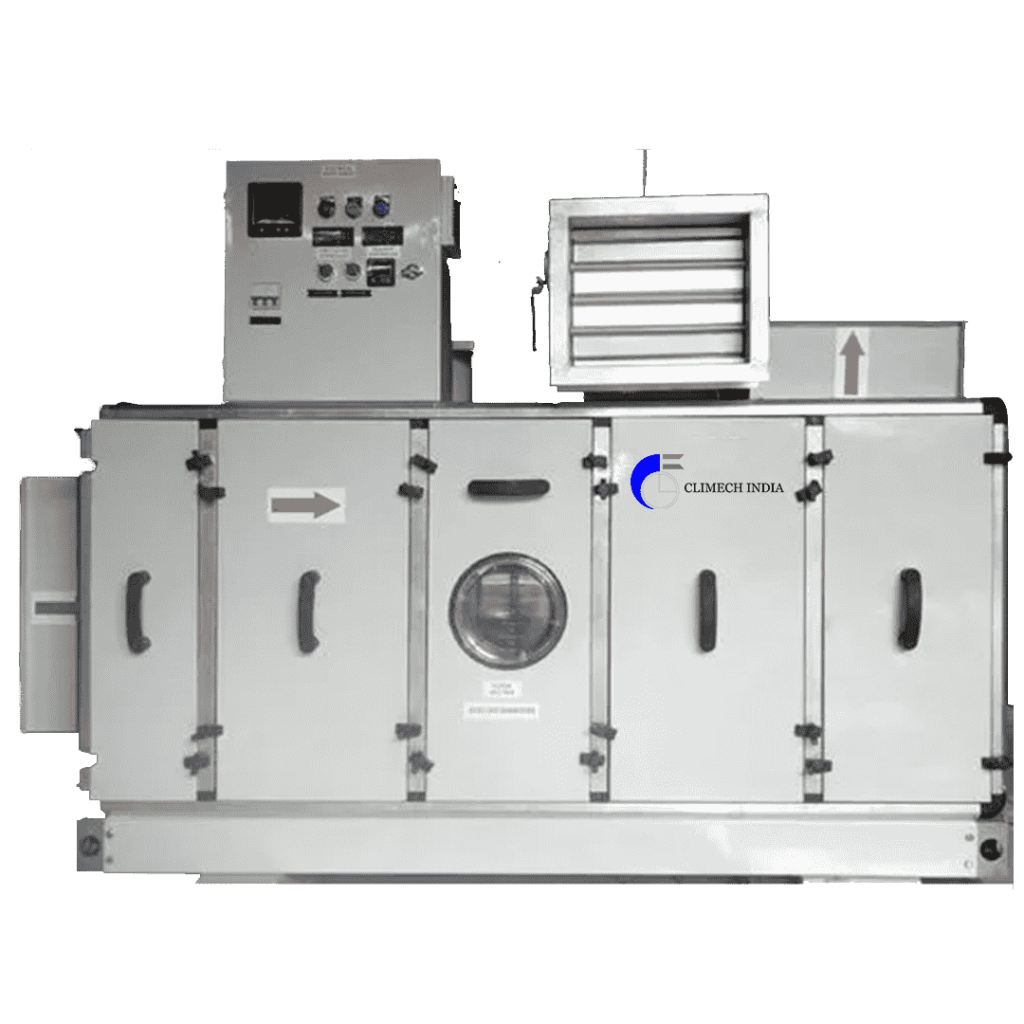
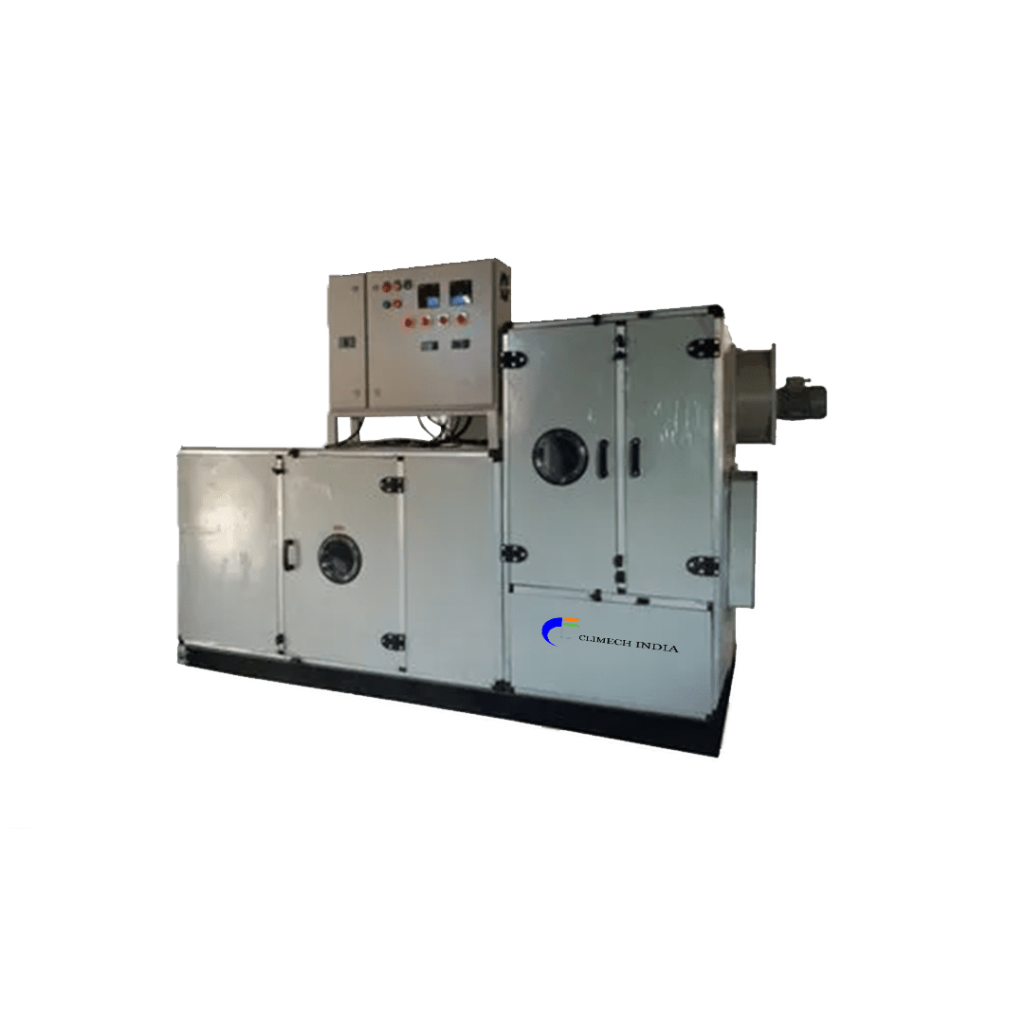
PRODUCT FEATURES
- Available in size form 100 CMH to 50,000 CMH
- Standard products include fully functional units with necessary safeties and electric relay based controls or optional PLC based Controller.
- Desiccant rotor technology removes water directly from the air.
- Designed for industrial process, including low dew point applications.
- Available with integrated pre and post cooling systems
- fast , simple access to all electrical and mechanical components through hinged doors or removable access panels
- Desiccant cassette can be removed for cleaning to extend rotor life and efficiency
- Choice of Gas, Steam and Electric Reactivation
- Standard features include easy access inlet filters, self adjusting /tensioning rotor drive components and easy seal adjustment .
- Robust industrial duty structural frame and panel design
- Highly compact design-lowest foot print area.
- fully factory assembled, reduced installation time on site and lesser costs.
OPERATING PRINCIPLE
- CLIMECH INDIA dehumidifiers operate on the principle of adsorption of water vapor from the air. The desiccant used is silica gel, which is formed on an inorganic substance.
- The desiccant and substrate are arranged in a wheel-shaped rotor matrix having thousands of small parallel air passages extending through its thickness.
- The desiccant rotor is housed in a cabinet that is separated into process and reactivation sections. In the process section, moist air passes through the rotor, and the silica gel adsorbs the moisture
- To drive the absorbed moisture out of the desiccante, the rotor slowly rotates into the reactivation section, where a second heated air is usually exhausted outside. The reactivated desiccant rotor rotates back into process section to provide continuous drying of the process air.
- In many applications, the process air is cooled before entering the desiccant rotor the enable the system to produce dry air. The reactivation air stream may be heated by electricity, steam, hot water , or natural gas depending on the application and available utilities